テキストと写真の共有で、お客さまへの対応スピードが大幅アップ
製造現場から各部門へ「direct」で情報発信
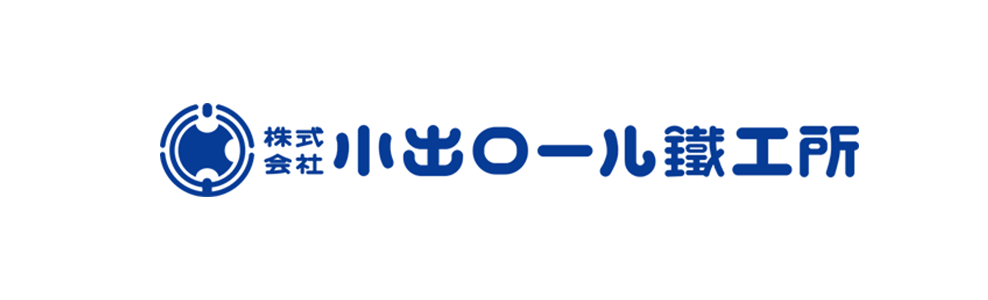
株式会社小出ロール鐵工所
- 常務取締役
小出 恵亮 様
- 品質管理部 設計課 課長
平林 隆志 様
株式会社小出ロール鐵工所は、大正3年(1914年)に東京都墨田区の地で生まれた100年以上の実績をもつ企業です。主に製鉄・製紙・印刷・食品などの生産に使われているロール・シャフトの製作、メンテンス、補修をおこなっています。
取り扱うロールは製鉄向けや自動車用鋼板向けの圧延ロール、印刷機器のガイドロールなどさまざまなものがあります。街で見かける道路の縞鋼板(しまこうはん)や自動車の鋼板、ラップ・アルミホイルなどの食品用フィルムなどは、これらのロールを使って製造過程で薄く伸ばして、私たちの身近な生活用品として使われています。
100年以上にわたって蓄積されたネットワークと製造加工ノウハウは、ベテラン従業員から若手従業員へ継承できるよう体系的なプログラムを取り入れており、全従業員が国家技能検定の取得に取り組んでいます。「より良い製品をスピーディーにお届けする」ことを基本方針としており、品質向上とお客さまへの対応スピードを非常に重視しています。その取り組みの中で「direct」がどのように活用されているのかをお伺いしました。
POINT
課題
導入の
決め手
活用・効果
従業員が確認・対応までに多くの時間を要していた
情報連携の効率化を期待して「direct」を導入
当社ではロールの材料調達から製造、運搬、設置、メンテナンスまでおこなっており、お客さまの要望に応じて一括受注からスポット受注までお受けしています。創業当初から基本方針として掲げている『より良い製品をスピーディーにお届けする』をモットーに、お客さまからの問い合わせや社内からの製造工程確認などの情報連携を効率化させるための取り組みをおこなっています。
メールや電話でやりとりしていた頃は、情報を発信してから従業員が確認・対応するまでに時間がかかってしまうことに課題を感じていました。ロールのメンテナンスで問題が発生した場合、すぐに確認して担当営業や取引先へ連絡をする必要があります。まずは製造部から品質管理部へ「ロールに疵があります。どうしましょうか?」と連絡が入り、品質管理部が工場に足を運び問題箇所をデジカメで撮影します。そして撮影したデータをPCに取り込んでから営業メンバーや取引先のお客さまにメールや電話で報告するという多段階的なやりとりをする必要があり、タイムラグが生じていました。
情報伝達の効率化を実現するITソリューションを探していたところ、ビジネスチャット「direct」の紹介を受けました。プライベートとビジネスを分けることができ、さらにはセキュリティ機能も万全ということですぐに導入しました。
事務職や営業部、管理部を中心とした一部の従業員同士の業務報告ツールとして運用を始め、操作が簡単なのでほとんどの従業員が問題なく利用できました。現在では、勤怠報告から作業報告、社長からの情報周知、雑談など、社内のさまざまなやりとりで活用しています。
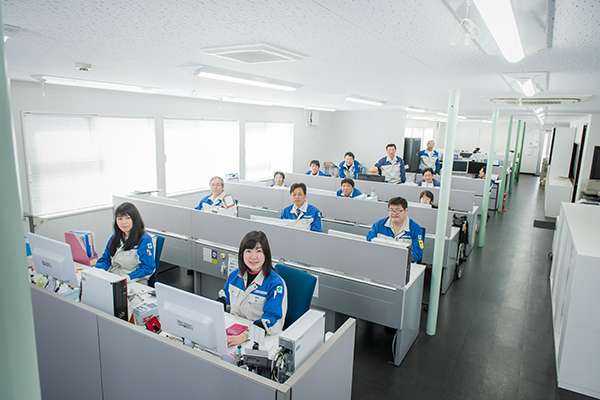
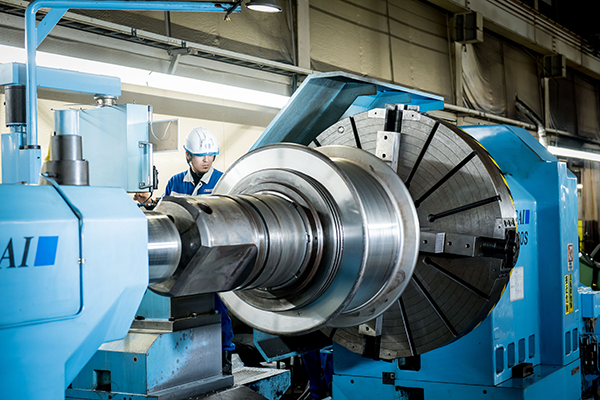
確認スピードUPと情報伝達の効率化を実感
ベテラン従業員のノウハウは「direct」で資産化活用
「direct」導入後、外出の多い営業メンバーへの連絡や確認は、あらかじめトークにメッセージを送っておけば、急ぎの場合でもすぐに連絡が取れるようになりました。「direct」はすべてのやりとりの既読・未読状況がメンバーごとに確認できるので、伝えたい人にきちんと情報が届いたのかを把握できるようになったのは評価が高い点だと思います。
また「direct」のグループトークでやりとりした内容は、後から追加されたメンバーもさかのぼって閲覧できます。ベテラン従業員のノウハウが蓄積されたトークに新しい従業員を追加することで技術情報の共有ができるため、従業員教育の効率化にもつながっています。
一回使ったロールをメンテナンスする場合、工程途中で何らかの問題が発生することがあります。そういった場合もすぐにお客さまや担当営業に伝えないといけないため、「direct」でスピーディーに連絡が取れるようにしています。
製造現場のやりとりは、メッセージと写真で状況把握
製造現場のやりとりは文字だけでは伝わりづらいことも多いため、よく写真を使用します。テキストの情報にビジュアルによる報告を加えることで、情報を受け取る側も内容を把握しやすく社内でもとても評価が高いです。
海外での立ち会い検査で海外から連絡するときも、「寸法精度がこうなっているからどうしましょうか?」という相談を写真とテキストで送信することで、お客さまからの指示を受けやすくなりました。製品の寸法的な検査も、検査状況を写真で送ってその場で判断できるため、時間をかけず適切な対応ができるようになりました。
テレワークを導入し「GPS勤怠ボット」を活用
当社は新型コロナウイルス感染症(COVID-19)拡大防止のため、テレワークを採用中です。
そのため自宅や離れた場所で業務をする従業員の勤怠管理は、「GPS勤怠ボット」を使って管理しています。一日の作業開始時間・作業終了時間・位置情報の報告はボットを介して回答するだけで、作業実績をExcel®ファイルで出力してくれるので、とても効率がよく使いやすいです。これは非常に助かっています。
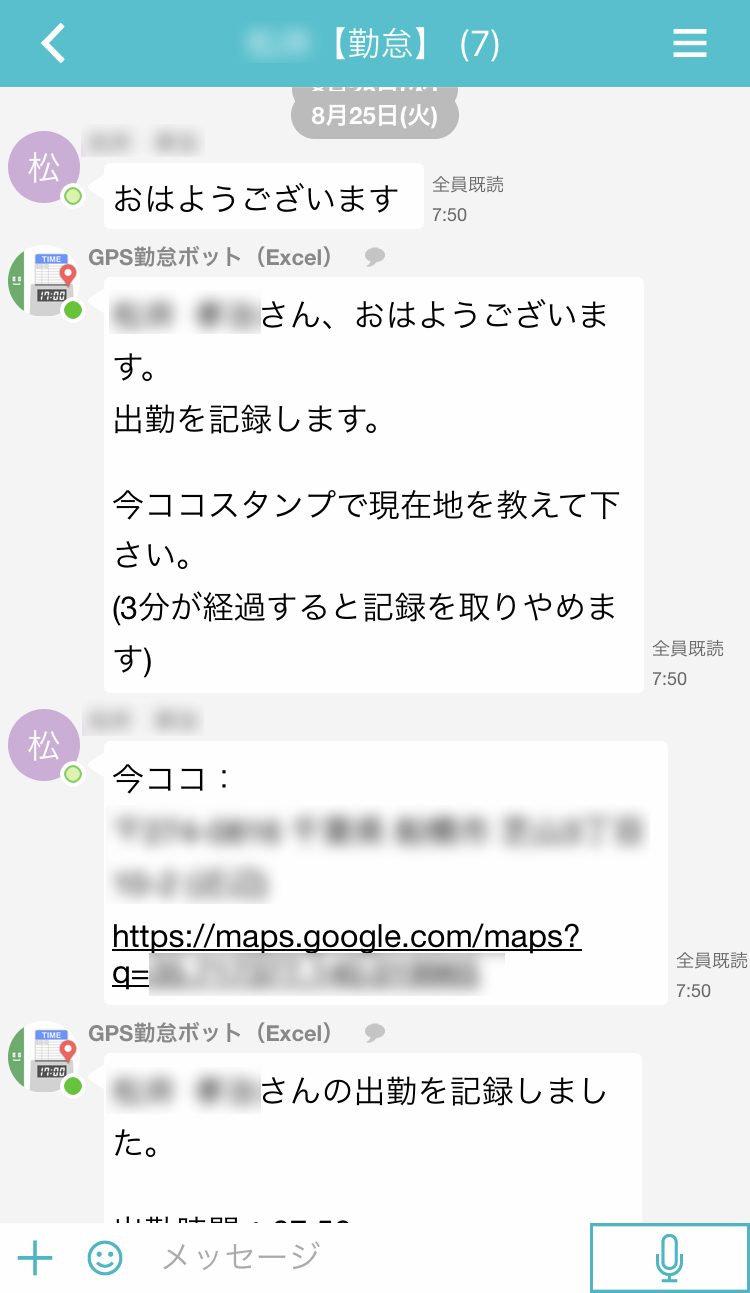
製造現場からも「direct」で情報発信し
情報共有のさらなるスピードアップと工程管理の効率化を目指す
工場で問題が発生した際、生産管理部門や品質管理部門を介して、営業メンバーにできるだけ早く連絡を取ってお客さまに報告することが必要とされています。そのため製造現場でも「direct」を使えるようにし、確認や問題が発生した時は工場からすぐに営業メンバーへ連絡が取れる様になり情報共有のスピードが大幅に向上しました。
「direct」は図面を確認できるため、本社工場でも「direct」を設置して製造工程の管理ができるようにテスト的に運用しています。そうすることで工程管理を効率化でき、生産性が向上できることを期待しています。
工場と営業メンバーとの情報を強化してお客さま対応のさらなるスピードアップを目指し、「direct」を今後も活用していきたいと思います。
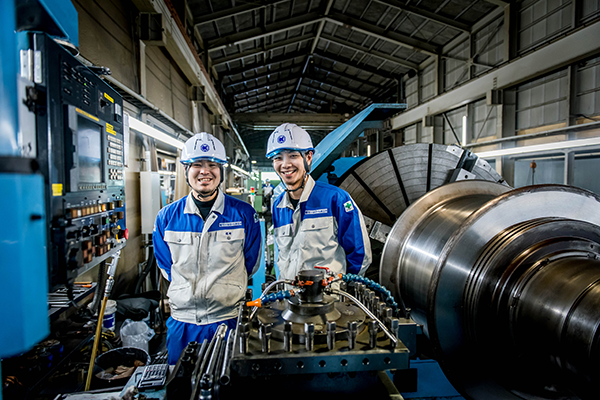
※記載内容は2020年8月時点のものです。